What to Expect from OSHA’s National Emphasis Program on Outdoor & Indoor Heat Hazards
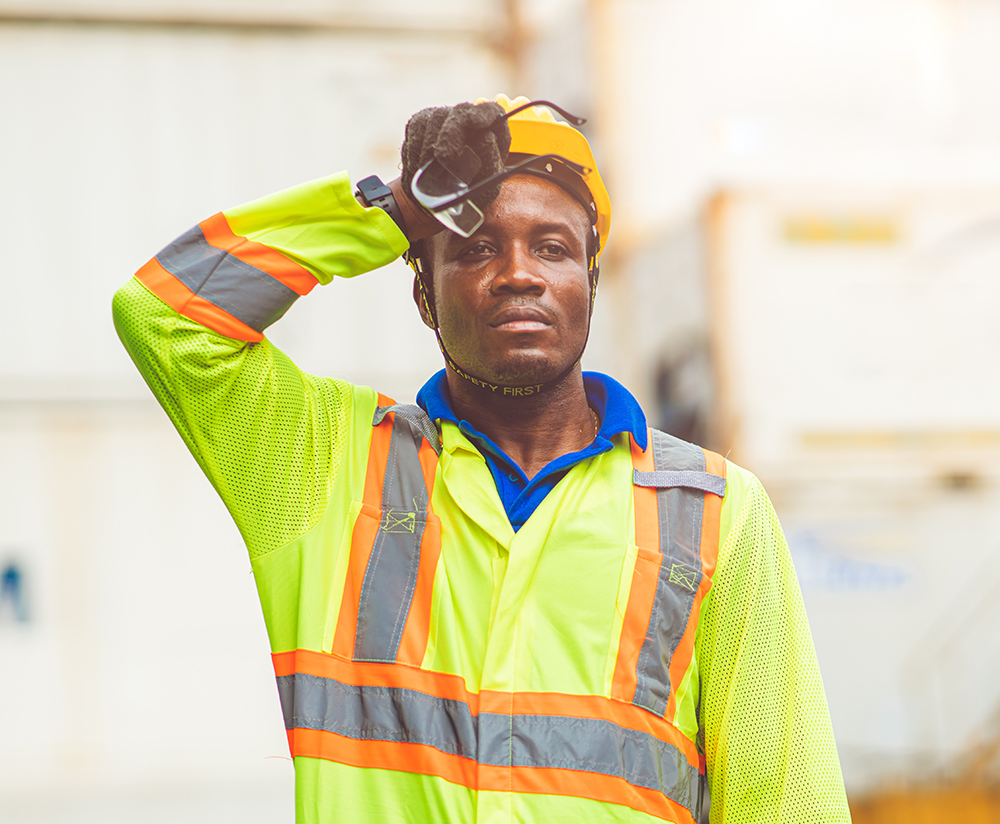
This blog article has been extracted from the Safeopedia webinar, "The Heat is On: What to Expect From OSHA’s New NEP on Outdoor & Indoor Heat Hazards" sponsored by Sqwincher, and can be viewed here. It is republished with permission.
What is a National Emphasis Program?
OSHA’s National Emphasis Programs (NEPs) are temporary programs that focus the agency’s resources on particular hazards and at-risk industries. OSHA’s NEP was launched on April 8, 2022 to drive the development of the first ever Federal Heat Standard to protect millions of workers from heat-related illness & death. Building upon OSHA’s ongoing initiatives, the NEP greenlights OSHA to conduct heat-related inspections on high-risk worksites while encouraging protective measures such as training, acclimatization procedures, and access to water (consider a fluid with electrolytes to boost the minerals in the body), rest and shade. The NEP will last for at least three years or until the Standard is released. The average Federal Standard takes seven years to develop.
Why Now?
There are various reasons for why the NEP was launched including:
- Climate change is increasing the danger of extreme heat
- 18 of the last 19 summers were the hottest on record
- Workers suffer over 3500 heat-related illnesses and injuries each year
- Unproportioned number of injuries among minorities
What Industries Will be Affected?
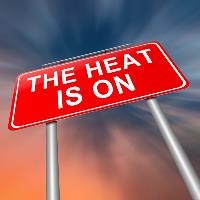
The NEP targets over 70 high-risk outdoor and indoor industries, primarily within construction and manufacturing where exposure is particularly high. Other primary industries include Residential & Commercial Building, Utilities, Roadwork, Civil Engineering, Contractors, Manufacturing, Farming, Automotive and Warehousing & Storage. These targeted industries were selected based on recent heat-related incident data recorded by the Bureau of Labor Statistics, as well as the highest number of OSHA heat inspections and OSHA general duty clause violations/hazard alert letters over a 5-year period. For a full list of industries affected reference Appendix A of the NEP.
What to Expect from the NEP
Compliance safety and health officers will initiate inspections on days the National Weather Service has announced a heat warning or advisory for the local area. If the heat index is 80°F or higher, inspectors and compliance specialists will engage in outreach and technical assistance to help keep workers safe.When all elements of a violation are established, Area Directors are responsible for issuing citations for hazards under the General Duty Clause. Hazard Alert Letters (HALs) may also be sent.
OSHA’s inspections will consist of a review of injury and illness logs and incident reports, a review records of emergency room visits and/or ambulance transport, interviews with workers for heat illness symptoms of dehydration, determining if the employer maintains a heat illness and injury prevention program and is documenting relevant conditions, such as the heat index, NWS heat alerts, type of heat source, exertion level and duration of exposure to heat. Inspection sites will be chosen at random on high heat days.
How Can Employers Best Protect Themselves and Their Employees?
Occupational heat stress is the net load to which a worker is exposed from the combined contributions of metabolic heat, environmental factors, and clothing worn which results in an increase in heat storage in the body. Occupational factors include: High heat index, low fluid consumption, direct sun exposure, limited air movement, physical exertion and PPE clothing and equipment.
Under OSHA law, employers are responsible for providing workplaces free of known safety hazards. This includes protecting workers from extreme heat. Employers must ensure that their safety policies address heat-related hazards, implement acclimatization periods for new employees, develop a means to monitor the heat index and employee exposure to heat and train employees on heat-related illness and emergency response.
An employer with workers exposed to high temperatures should establish a complete heat illness prevention program. Key elements to a successful heat illness prevention program include: Identifying a dedicated person and hazard ID, encouraging hydration, (consider a fluid with electrolytes to boost the minerals in the body), rest and shade and modifying work schedules accordingly. Employers should provide ample training and monitor their employees, in addition to implementing an emergency response plan.
How Can Employees Keep Themselves Safe from Occupational Heat Stress?
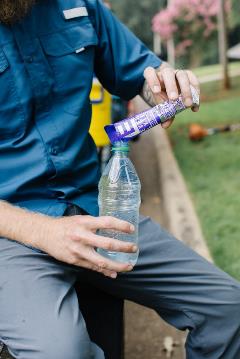
- Become aware of the signs and symptoms of heat-related illnesses: Learn the signs and symptoms of heat exhaustion and heat stroke, which can include fatigue, nausea, headache, dizziness, and confusion. If you experience any of these symptoms, it’s important to seek medical attention immediately.
- Stay hydrated: Drink plenty of fluids. A proper regimen of water and Sqwincher® electrolyte replenishment, before, during, and after working in high heat environments to help prevent and/or recover from dehydration. Avoid drinks that contain caffeine, alcohol, or excessive sugar.
- Wear appropriate clothing: Wear light-colored, loose-fitting clothing that covers as much skin as possible. Choose fabrics that are breathable and can wick moisture away from the skin.
- Take breaks and rest in a cool area: Take frequent breaks and rest in a cool area to help regulate your body temperature. Use fans or air conditioning, if available.
- Follow your employer’s heat safety plan: Your employer should have a heat safety plan in place that includes measures such as providing water and rest breaks, monitoring workers for signs of heat-related illness, and adjusting work schedules to avoid working during the hottest parts of the day. Follow these measures and report concerns to your supervisor.
Connect with Saf-T-Gard to Learn More
Industrial safety is our legacy going back 9 decades. For an overview of our Sqwincher® Hydration Solutions, please visit Sqwincher.