The ABCs of How to Properly Care for Rubber Insulating Goods for Continued Safety, Usage, Compliance, and Cost Savings
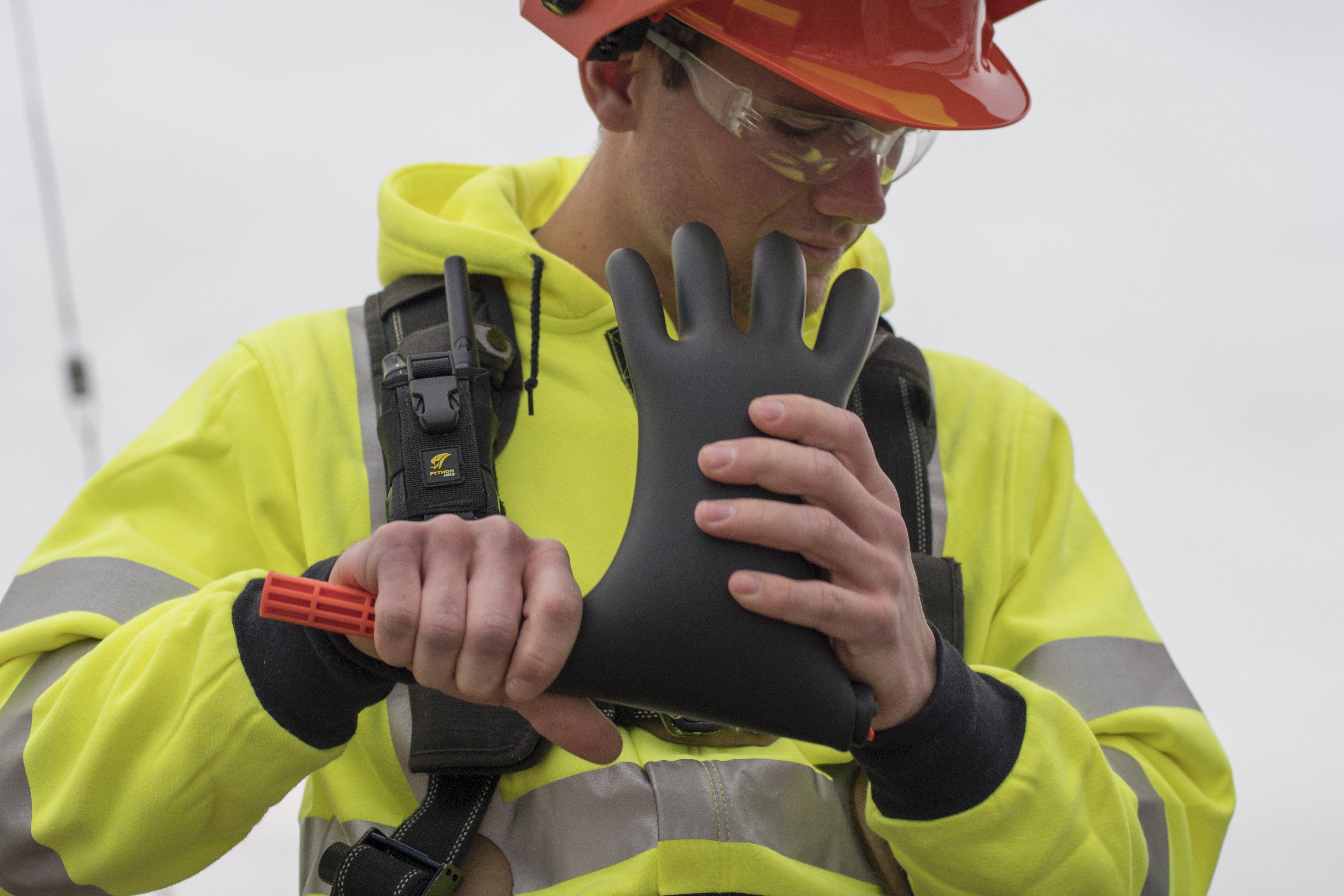
A – Always Inspect before Use!
ASTM F496-24 Standard Specification for In-Service Care of Insulating Gloves and Sleeves requires the regular inspection of in-service electrical protective equipment in order to maintain compliance and ensure the products’ safety and integrity when exposed to energized equipment and power lines. Similar standards exist for other rubber insulating products. All rubber insulating products should be thoroughly inspected prior to use. Common problems to look for include the following:
- Cracking and Cutting – Prolonged folding or compressing can cause this type of rubber damage.
- UV Checking – Storing in areas exposed to prolonged sunlight causes UV checking.
- Chemical Attack – Oils and petroleum compounds can cause swelling of the rubber.
- Avoid Folding – The strain on rubber at a folded point is equal to stretching the rubber to twice its length.
- Snags – Wood, metal splinters and other sharp objects can snag or tear rubber.
- Physical Damage – Rope burns, deep cuts, and puncture hazards are cause for rejection.
Visually inspecting rubber insulating gloves, rubber insulating sleeves, and rubber insulating blankets identifies physical, chemical or ozone damage. Direct light is recommended because it enhances the ability to see surface imperfections on the rubber. Inflating the rubber insulating gloves with air or otherwise stretching the surface helps identify age and ozone damage as well as other physical damage such as snags, rope burns, deep cuts, and punctures. A portable, mechanical inflator may be used in the field to enhance the inspection of the rubber insulating glove and identification of any damage. Simply affix the rubber insulating glove to the inflator and pump it up to view any damage to the rubber insulating glove that is not otherwise visible unless viewed after inflating.
Otherwise, if portable inflator is not available, use a rubber glove inspection tool or roll the rubber insulating glove cuff tightly to trap air inside. Expand the rubber insulating gloves no more than 1.50 times their normal size for Type I non-ozone-resistant rubber. Listen for any escaping air to detect holes. Then, apply pressure to areas of the rubber insulating glove to inspect for escaping air. Repeat the procedure again with the rubber insulating gloves turned inside out.
The use of two-color rubber insulating gloves can also aid in the identification of problems in that any damage to the outer layer enables the inner, contrasting color to be seen.
When inspecting rubber insulating sleeves, make sure to examine them along the edge as they are rolled. Rolling will stretch the rubber insulating sleeve along the edge, making cuts, tears, and ozone cutting more visible. Repeat this process again with the rubber insulating sleeve turned inside out.
Roll rubber insulating blankets to properly inspect them in order to locate scratches, tears, abrasions, snags, corona cutting, or age cracking. Make sure to roll the rubber insulating blankets two times on each side, with the second roll at a right angle to the first. Immediately remove rubber insulating blankets from service that show any signs of damage.
Make certain to thoroughly inspect rubber insulating line hose, hoods, and covers inside and out for cuts, scratches, corona cutting, holes, tears and punctures, aging, rope or wire burns, and texture changes such as swelling, softening, hardening, becoming sticky, or inelastic.
B – Be Compliant!
OSHA 29 CFR 1910.137(b) covers in-service care and use of electrical protective equipment, specifically rubber insulating blankets, covers, line hose, gloves, and sleeves and specifically references the relevant ASTM specifications:
- ASTM F478-14a (2023) (Rubber Insulating Line Hose and Covers)
- ASTM F479-06 (2022) (Rubber Insulating Blankets)
- ASTM F496-24 (Rubber Insulating Gloves and Sleeves)
While regular inspection of in-service rubber insulating products is included as part of OSHA 29 CFR 1910.137(b) and ASTM specifications regarding in-service use and care of electrical protective equipment, this section on compliance is going to focus specifically on electrical testing.
Although damage to many types of personal protective equipment (PPE) can be apparent when the equipment or devices are inspected by the user, rubber insulating products are more complicated. The reduction in effectiveness can be caused by a variety of factors that may not be readily apparent to the user. Improper use of rubber insulating products can be a matter of life or death, which is why dielectric testing is a critical and necessary component to maintaining worker safety and compliance. Moreover, rubber insulating products are costly, and many times these costs are unnecessarily increased by purchasing replacements for rubber insulating products that could have remained in-service with the proper testing and recertification.
Various ASTM Manufacturing and Acceptance standards mandate the testing of the rubber insulating products by the manufacturer or supplier prior to the first delivery to the end user. End users (or an end users’ designee) may perform acceptance testing within the first two months after receipt and prior to placing rubber insulating products into service. Once placed into service, there are periodic retest intervals specified in the following ASTM standards:
- ASTM F496 Rubber Insulating Gloves – Six (6) months (except for industries such as telecommunications that utilize rubber insulating gloves as a precautionary protection, in which case the maximum interval may increase to nine (9) months)
- ASTM F496 Rubber Insulating Sleeves – Twelve (12) months
- ASTM F479 Rubber Insulating Blankets – Twelve (12) months
- ASTM F478 Line Hose and Covers – When field inspection or company policy warrant
These in-service retest intervals are the MAXIMUM permitted and in addition to the daily field care and inspection. It is quite common for users, including power utilities and contractors, to specify shorter intervals. However, do not place rubber insulating products into service unless they have been electrically tested within the previous 12 months.
If you do not have the equipment required to perform these electrical tests, there are independent accredited testing facilities that can perform the acceptance and in-service testing on behalf of end users. At a minimum, ASTM standards require that the inspection and testing process include the following steps:
- Check-in
- Removing previous testing marking
- Washing using cleaning agents that will not degrade the insulating properties
- Visual inspection of all surfaces (inside and out)
- Electrical test
- Final inspection
- Recordkeeping
- Marking
- Packing in appropriate containers (“appropriate containers” means boxes, or similar sturdy packaging materials to prevent folding, creasing or similar loose storage that can cause stress on the rubber) for storage or shipment
When selecting a test lab for use, make sure that it is a NAIL-accredited test lab. NAIL stands for North American Independent Laboratories for Protective Equipment Testing (www.nail4pet.org). It incorporates the only Laboratory Accreditation for the electrical equipment test labs program in North America. NAIL4PET helps develop uniformity in testing and works in close association with the American Society of Testing Materials (ASTM International).
C – Consult the Experts!
With all the different problems to look for when inspecting rubber insulating products coupled with all the various testing intervals to remember as well as all of the required inspection and testing process steps to consider, it’s easy to see how compliance can fall through the cracks. Consider partnering with an electrical test lab that can test your rubber insulating products and manage the rubber insulating products change-out process for you. Keeping these services bundled together under one roof will minimize out-of-service time and unburden you from the coordinating, organizing, inventorying, and scheduling of multiple rubber insulating product types, sizes, and quantities.
Saf-T-Gard's Voltgard® Test Lab can manage all of this for you! As the largest, independent, NAIL4PET-accredited test lab in the United States, the Voltgard® Test Lab performs full-service testing and recertification services for 12 different categories of rubber insulating products – all to the following applicable ASTM standards:
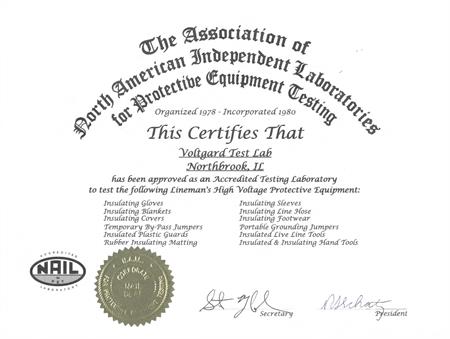
- Insulating Gloves ASTM D120, F496, F1236
- Insulating Sleeves ASTM D1051, F496, F1236
- Insulating Blankets ASTM D1048, F479, F1236
- Insulating Line Hose ASTM D1050, F478, F1236
- Insulating Covers ASTM D1049, F478, F1236
- Dielectric Overshoe Footwear ASTM F1116, F1117
- Insulating By-Pass Jumpers ASTM F2321, F2249
- Portable Grounding Jumpers ASTM F2249, F855
- Hot Sticks and Live Line Tools ASTM F711, IEEE 978, F1825, F1826
- Insulating Plastic Guards ASTM F712
- Insulating Hand Tools ASTM F1505
- Rubber Insulating Matting ASTM D178
Additionally, Saf-T-Gard developed the Voltgard® Original Rubber-Goods Change-Out Program®, the industry’s first structured, professionally-managed program, more than 30 years ago in response to customers’ needs and regulatory requirements. The Voltgard® Original Rubber-Goods Change-Out Program® provides a hassle-free, start-to-finish solution that monitors, tracks, and manages your rubber insulating products’ in-service use and testing intervals for you so that your workers can focus on other work priorities while staying safe, productive and compliant. Ideal for utilities, electrical contractors, cable and telecom providers, power and contractors, wind/solar energy, public transit, and other large users of rubber insulating products, the Voltgard® Original Rubber-Goods Change-Out Program® includes the following five key elements:
- Cleaning
- Visual inspection
- Electrical testing
- Markings according to your company’s safety protocols
- Shipment to your warehouse or jobsite when and where they are needed
Furthermore, Saf-T-Gard has one of the largest new rubber insulating products inventories in the worldand can immediately replace any goods not meeting applicable standards, including ASTM, OSHA, or your company’s own safety policies. No other test lab offers the Voltgard® level of service!
Connect with Saf-T-Gard to Learn More
Industrial safety is our legacy going back nine decades, and electrical safety is our specialty. The Saf-T-Gard and Voltgard® team has more than 100 combined years of safety expertise, focusing on industrial and electrical safety. Our team includes ASTM Voting Members, OSHA 30-hour trained safety professionals, Qualified Safety Sales Professionals (QSSP), and NFPA 70E trained safety professionals. The expertise and experience of our team can be an extension of your team when you partner with Saf-T-Gard on your company’s safety program.
For a limited time only, Saf-T-Gard is offering 10% off all electrical safety products purchased online in honor of National Electrical Safety Month. Just enter promo code NESM10 where prompted during the checkout to redeem. Offer expires May 31, 2025.For an overview of our electrical safety products, and to order for immediate shipment, please visit Electrical Safety. For an overview of the Voltgard® Test Lab and to request electrical testing services, please visit Send Us Your Electrical Safety PPE. For an overview of the Voltgard® Change-Out Program, please visit The Original Rubber Goods Change-Out Program®.